Spinning a digital thread for SPY-6
Digital engineering speeds system development, delivery and sustainment
It’s where two worlds meet – the digital and physical. It’s called digital transformation. And it’s changing how defense systems such as the AN/SPY-6(V) 1 radar, also called SPY-6, are engineered and produced at Raytheon, a Raytheon Technologies business.
SPY-6 is a family of advanced naval radars that can simultaneously detect and counter threats in the air and at sea. The multi-mission system is game-changing for fleets; it gives operators and commanders more time to react by identifying more threats faster and at farther distances.
Because speed to the battlefield is as important as speed on it, the business is looking to digital transformation to meet the mission.
“Digital engineering helps us design, develop and deliver advanced capabilities like SPY-6 faster, giving our customers a competitive edge that translates to saving more lives at the end of the day,” said Bryan Rosselli, vice president of Business Transformation and Execution at Raytheon.
The business has invested in advanced visualization with software that engineers can use to render detailed digital versions of products, parts, systems and subsystems. This, along with digital engineering technologies, such as artificial intelligence, machine learning, modeling and simulation, as well as software development methods, help grow efficiencies, boost quality, lower costs and improve time to the battlefield.
“We weave the digital thread throughout the entire product lifecycle, and it stays connected – from design to deployment in the field and extends to training, maintenance and sustainment,” said Michelle Serafini, operations manager of the Immersive Design Center at Raytheon.
Designing in a virtual environment
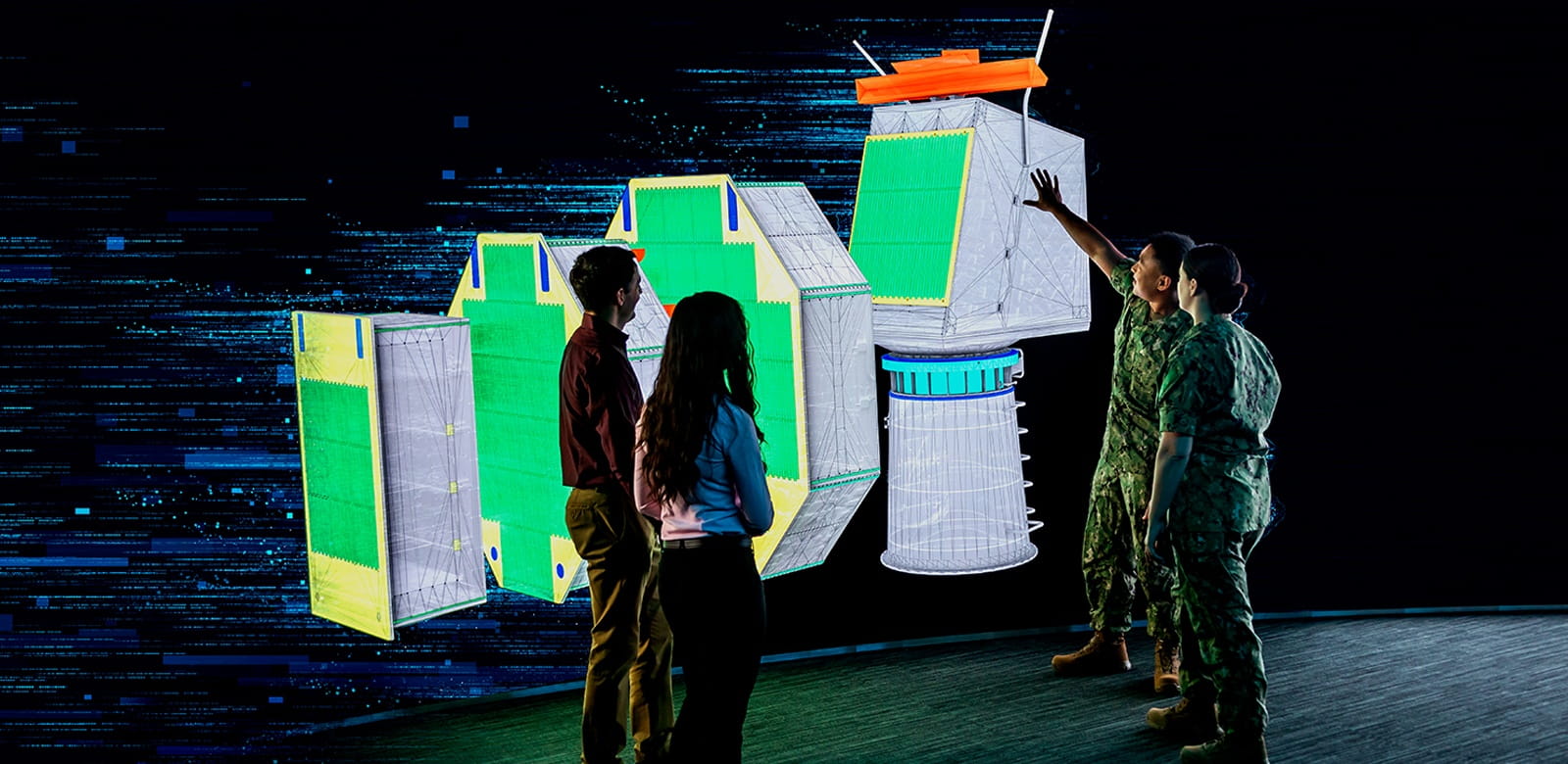
Raytheon uses digital technology to allow seamless sharing of information among people, machines and sensors.
The design process starts inside Raytheon’s Immersive Design Center in Andover, Massachusetts.
Inside, a 32-foot-long LED screen can display detailed renderings of pretty much anything Serafini wants to show. For example, users from all over the world can meet virtually – step inside a SPY-6 radar or board a ship equipped with one, visit the production factory or go to war. Wearing a HoloLens virtual reality headset, users in the facility or at home can even interact with a SPY-6 model. The company has five more of these facilities around the world in Tucson, Arizona; Fullerton, California; McKinney, Texas; Canberra, Australia; and Warsaw, Poland. And they all continue to evolve with the latest and greatest technologies.“With locations around the globe, teams can accomplish digital engineering reviews, share 2D and 3D data real-time, no matter where they’re located, increasing collaboration,” Serafini said. “We can have people remote at home, we can have our core group of people in different locations, and we can tie the centers together.”
Raytheon uses the Immersive Design Center for:
“We can take our customer’s specific terrain and paint the picture with their care abouts, adding in current assets and possible threats and really illustrate the benefit of having a layered defense system,” Serafini said. “We use high-fidelity modeling and simulation to conceive products.”
“Doing full-scale virtual reviews allows us to gain efficiencies, reducing our risks in our designs and improving them before we produce anything in the real world,” Serafini said. “And it allows our teams to come up with more innovative, robust solutions that work better for our customer and are more affordable.”
The Immersive Design Center also helped Raytheon configure its 30,000 square-foot Radar Development Facility in Andover, where the SPY-6 radar is produced.
“For SPY-6, this was very important because the arrays are giant, so we wanted to ensure there was room for the robots to lift and move things around properly,” Serafini said.
Producing with advanced manufacturing
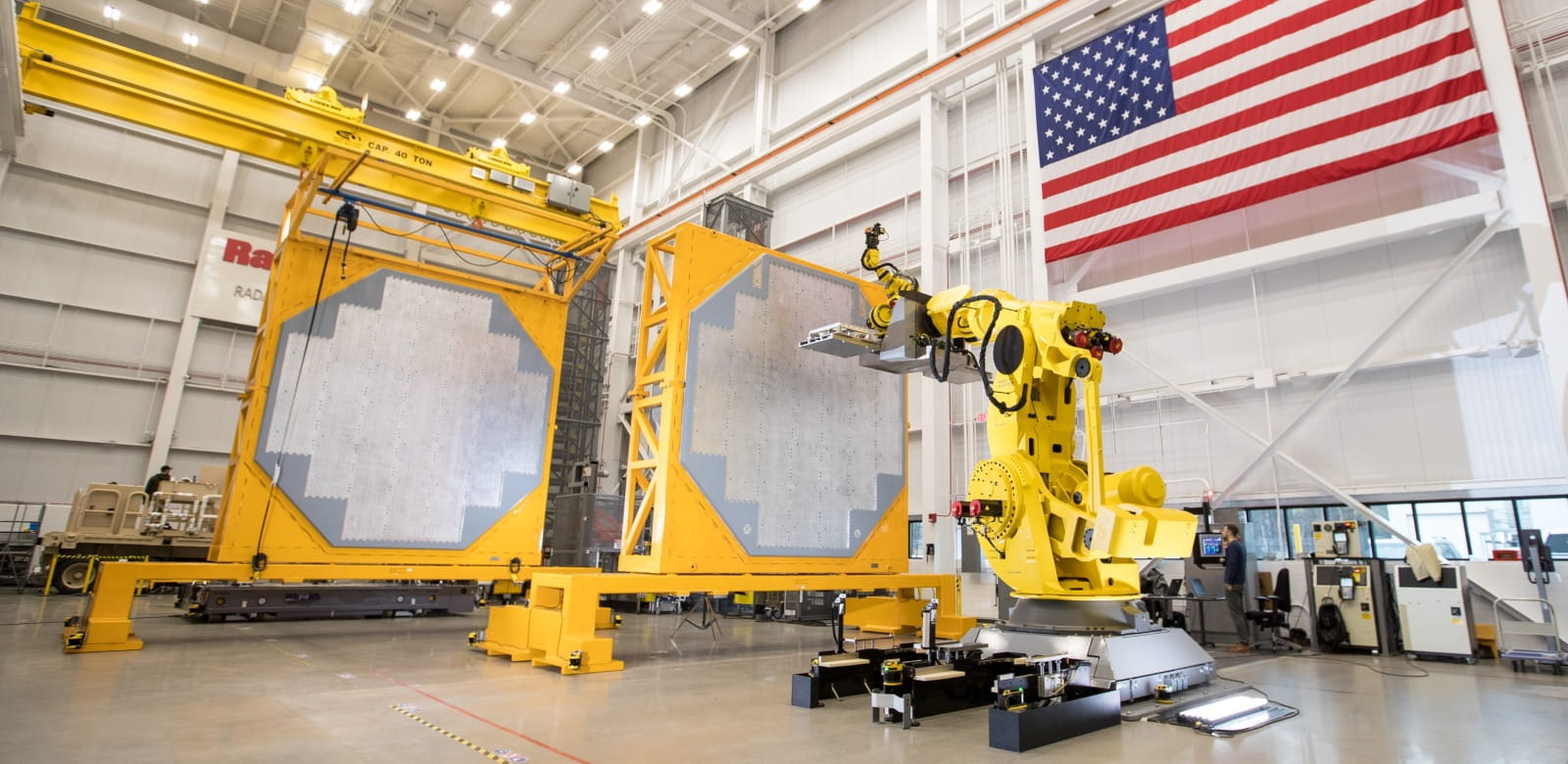
Raytheon tests a SPY-6 integrated air and missile defense radar inside its 30,000 square-foot Radar Development Facility in Andover, Massachusetts.
The Radar Development Facility is a “connected factory,” which means it uses digital technology for seamless sharing of information among people, machines and sensors, including suppliers.
To meet high-rate production, the business operates a vertically integrated factory, which supports multiple product lines and follows the same process for each, helping them to easily pivot from one system to another.
“As a leader in integration defense solutions, we bring together the best minds, systems and capabilities to create next-level solutions like SPY-6,” said Brendan Hamm, a program operations manager at Raytheon. “The digital thread and our vertically integrated factory help us do that.”
The business is also looking to automation to gain efficiencies and agility in their operations, using robots to perform assembly typically done by hand, and to conduct automated optical inspections.
“It’s more accurate and highly repeatable,” Hamm said.
Much of the automation happens around the clock – 24 hours a day and seven days a week, but that’s not taking away work. Instead, it’s changing people’s jobs.
And with a lot of moving parts in the massive factory, they use robots powered by AI to move systems from one location to next.
“We mapped out the entire factory, so the robots know what it looks like and will react if things change in the map,” Hamm said.
To help counteract some of the global supply challenges, the business is looking within, using its metal fabrication shop to make needed components, and it’s doing the same to produce its gallium nitride technology.
Another way the business is gaining efficiencies is with RFID technology, which streamlines production through real-time asset and materials tracking for factory floor visibility.
“We receive 500-600 packages a day through the dock, and it’s important that we be able to track each box as it moves around the factory,” Hamm said. “RFID tech offers factory floor visibility at your fingertips.”
Sustaining with innovation
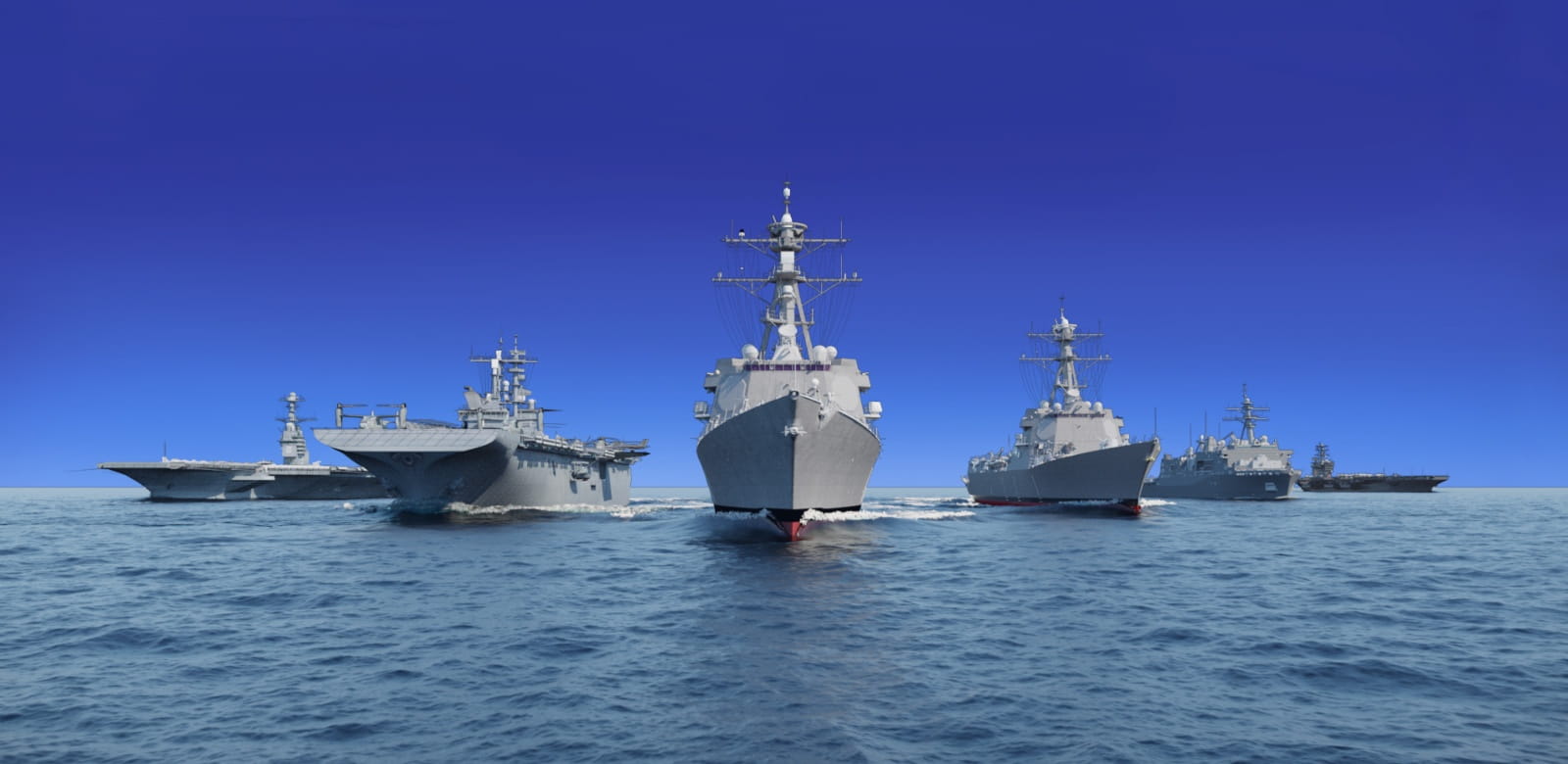
Raytheon uses agile DevSecOps—short for Development, Security and Operations—based surface combatant software development to revolutionize navies’ ability to respond to and outpace threats.
Basically, modern naval radars keep track of things – planes, missiles, drones and much more – that change constantly. So the software they use needs to change constantly as well – much faster than traditional military development cycles would ever allow.
Agile software development techniques are being used to innovate and iterate quickly, helping navies update their fleets to stay ahead of threats.
Raytheon offers software development methods like agile and DevSecOps, along with cloud computing architectures, to continually develop, integrate, test and deliver capabilities for SPY-6 iteratively – sometimes even in days.
Developers can create a basic version of a capability, then improve it quickly and continuously, much like commercial tech companies frequently add features and functions to smartphones and apps.
Another way the business is sustaining SPY-6 is by installing new hardware onto existing naval destroyers. But before those upgrades are made in real-life, they’ve been reviewed and made in a virtual environment using 3D digital twins, laser-scanned data and an avatar.
“Ships have limited space, so we must ensure that systems fit and connect properly, and that people can access the space, for example, to reach and connect cables to do an update,” Serafini said. “It’s important that nothing is off.”
Hardware and software updates like these inject new and improved functionality into SPY-6.
“They help extend the life of the system, giving customers advanced capabilities, but more importantly, they save lives,” Serafini said.