Raytheon Technologies opens high-tech ‘factory of the future’ in North Texas
Company announces growing manufacturing presence in region
Time-lapse video shows the construction of Raytheon Intelligence & Space’s new Advanced Integration and Manufacturing Center, a 178,000 square-foot facility in McKinney, Texas.
The new factory was months away from being finished, but its designers needed to know right away how the workers would like the new layout.
So they let them in – not to the construction site, but to an exact digital replica.
The team’s ability to do a virtual test run – and make quick, valuable layout changes – is just one example of the innovative mindset behind Raytheon Intelligence & Space’s new Advanced Integration and Manufacturing Center, a 178,000 square-foot facility in McKinney, Texas, that will produce futuristic defense technologies including imaging equipment and high-energy laser weapon systems.
“It’s our business to tackle the world’s hardest problems, and we must stay open to new ways of doing things to ensure that we meet our customer commitments with agility and speed,” said Jeff Place, vice president of Operations & Supply Chain for RI&S, a Raytheon Technologies business.
The center, which officially opened in September 2021, is the foundation of Raytheon Intelligence & Space’s growing investment in high-tech manufacturing in McKinney; the company also announced that it will build more state-of-the-art production facilities in North Texas by 2025.
About the new AIM Center
The AIM center is the product of a $100 million investment made in collaboration with the McKinney Economic Development Corporation. RI&S has fulfilled a pledge to support 500 new skilled jobs in connection with the project.
Built to help quickly and efficiently meet growing customer demand, the facility is as cutting edge as the technology that will be made on the factory floor.
“Smart factory” initiatives use real-time data, automation and connected tools to ensure, for instance, that ovens used to cure adhesives meet product temperature and time requirements. The “clean sheet” design makes efficient use of space, enabling key materials to travel 80% less and ultimately allowing sensor turrets and other products to reach troops in the field faster.
In an environment where a microscopic speck of dust can degrade performance of sensitive optical equipment, a next-level ISO 7 clean room keeps out virtually all airborne particles, down to 0.5 μm – about the size of one-tenth of a red blood cell.
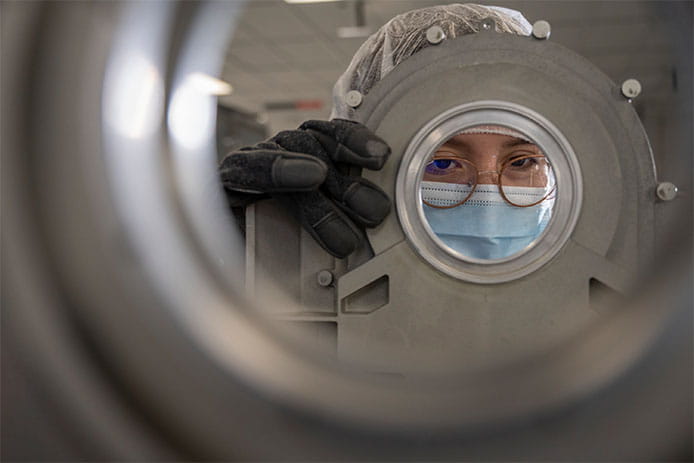
A Raytheon Intelligence & Space technician places pieces of the outer shell of a Multi-Spectral Targeting System into a small oven during the assembly process in the new AIM Center.
The AIM Center is only the beginning, too.
RI&S in September also announced it will build more state-of-the-art manufacturing capabilities in McKinney by 2025. The new project will deliver even more advanced technology to RI&S’ customers and generate an additional 700 skilled jobs.
“These investments will serve as a model for RI&S’ digital transformation,” said Place. “We’re investing in high-tech manufacturing and our people to make it faster, easier and more affordable to put disruptive technology in our customers’ hands.”
That transformation entails reinventing the business to bring faster delivery cycles and create more powerful innovations to develop and deploy new products quicker than ever before.
In that digital practice run last year, for instance, the immediate benefit became apparent as soon as the team arrived at a key product testing area. Specifically, the operators quickly realized they needed an extra wall.
The design-build team responded accordingly, making that tweak on the fly during construction, when changes are cheaper and easier.
“We really did treat it like the same kind of process you would go through to design a new product – and it paid off,” said Alicia Clark, an RI&S senior project manager, who has been leading the AIM Center’s creation.
The RI&S team added in precision and sophistication at every step. The business enlisted the help of its in-house experts in building sophisticated products to bring those same techniques into the construction of a facility, which will make those very products.
They even pulled in Porsche Consulting – the luxury sports car experts – for insight on how best to build a masterpiece manufacturing facility that can create exquisite products while also accommodating growth.
The approach reflected the desire of RI&S’ business leadership to build a center marked by sweeping changes, rather than incremental improvements over existing facilities.
“One of the things the AIM Center did was pull together what is possible and put them in one place,” said LeAnna Kopydlowski, RI&S’ AIM Center design lead.
A 3D digital model allowed designers to better visualize the space in its conceptual stages, much the way product designers model and simulate a product design.
The team then deployed a laser scanner throughout the building process to take thousands of scans totaling more than 10 terabytes of data. The result was a true digital replica – one that could even see through walls to view every wire, pipe and other minute detail in the facility.
That confidence in design is important because the AIM Center, which saw some workers start using the space earlier this year, was built to put people at the forefront.
Factory employees never have to go more than six feet to grab a necessary tool or complete a key task. Technological improvements include automated torque controllers and an RFID grid. The new clean room simultaneously controls humidity, temperature and cleanliness. Ergonomics and safety are built in, and open, modular designs mean that the people doing the work can better collaborate, communicate and innovate to deliver on commitments.
“The AIM Center puts the product and the people at the center of the design,” said Kelly Dodds, RI&S’ advanced manufacturing tech director. “We all understand the importance of our mission and that each of us plays a part in delivering for the ones who keep us safe.”