Simulating the sea
At a seaside site in Rhode Island, specialized labs help Raytheon’s Advanced Technology business test underwater innovations
A sleek, silver unmanned vehicle patrols the depths, using sound waves to scan its surroundings and identify objects nearby. When it finds a mine, it takes a picture with its advanced camera system and sends it to a human operator in a safe location for confirmation.
Then, the vehicle known as Barracuda does something no other mine neutralizer can.
As the mine drifts with the current, Barracuda starts swimming in sync. It uses its four impellers to twist and turn, matching the mine’s movement.
Then it lines up a shot and destroys its target.
“It can go up, down, sideways. It can do alligator rolls,” said Lionel Boisvert, director of sensors for Raytheon’s Advanced Technology business. “It's like an underwater ballet.”
Hear a Barracuda in motion
Raytheon, an RTX business, invented Barracuda in Portsmouth, Rhode Island – the company’s center for undersea research, and the point of origin for many sonars, torpedoes, undersea vehicles and mine detection equipment for U.S. and allied navies.
The story of Barracuda is, in miniature, the story of Raytheon's Advanced Technology business – a group of innovators that for years has matured technologies that other Raytheon teams incorporate into products. Today, they’ve taken that a step farther, and are incorporating their work into products of their own.
“We work with science and technology customers in the Department of Defense to create amazing new technologies that we can utilize in our products five, 10, or 20 years down the line,” Boisvert said. “Really across Raytheon Advanced Technology, our mission in life is to create technology breakthroughs that deliver an advantage. Here in Portsmouth, we've worked on a number of technologies over the years to be able to do exactly that.”
Beyond its track record, what sets the Portsmouth site apart is its unique testing facilities, which allow engineers and researchers to simulate the harsh, punishing and otherwise difficult conditions their technology will encounter at sea.
“You put stuff under absolutely crushing pressures and deep cold, so how can you test that something’s going to stay at the bottom of the ocean for 40 years?” Boisvert said. “We have test facilities that enable us to test for things like that.”
How do you simulate the sea?
Raytheon’s Portsmouth, Rhode Island facility overlooks Narragansett Bay and tests technologies including radars that transmit across the ocean and sonars that operate far below the surface, where temperatures, pressures and other factors present challenges unlike any other environment.
Hear Lionel Boisvert explain the complex conditions and see how the team in Portsmouth can simulate them in their specialized labs:
In his words
Salinity
Temperature
Sound
Once products have been proven in the lab, the team can test them on-site in Narragansett Bay with one of several vessels. After development, many products are manufactured in the Portsmouth facility as well. The ability to take a product from research to manufacturing in one location helps speed production, ease scheduling and reduce the risk of damage in transit.
For anything they can’t test there, Boisvert said, they can work with the nearby Naval Undersea Warfare Center and universities.
“The more facilities that you can have that are unique, the better off you are. But there’s a cost trade-off there, of course, with space, maintenance, upkeep, and the expertise that's needed to actually run these facilities,” Boisvert said. “We’ve figured out the right balance of those particular test facilities and boats and other things to make sure that we're very cost competitive.”
Investing in the future
Under bright lights and yellow cranes hanging overhead, the acoustic test tank at the Portsmouth site stands out – even in a place whose purpose is to build revolutionary technology. Now, the team in charge of that tank is looking to do even more.
Until recently, they could test only one object at a time. While the tank was plenty big – 20 feet deep, and about as long as a school bus – the problem was isolation. Testing more than one object meant the sound waves would interfere with each other and skew the results. As the number of items waiting for a test grew, the team came up with a simple yet effective solution: A divider.
“It’s very hard to get scheduled tank time, so to speed up production and our engineering that we need to get done, this acoustic divider is going to allow us to test two different programs at a time,” said Abigail Fabian, one of the engineers upgrading the tank.
On top of that, she's also updating the software from a custom-built ’90s-era app to a modern version that’s widely used.
All told, the improvements will make the tank easier to use and modify as the site’s needs grow.
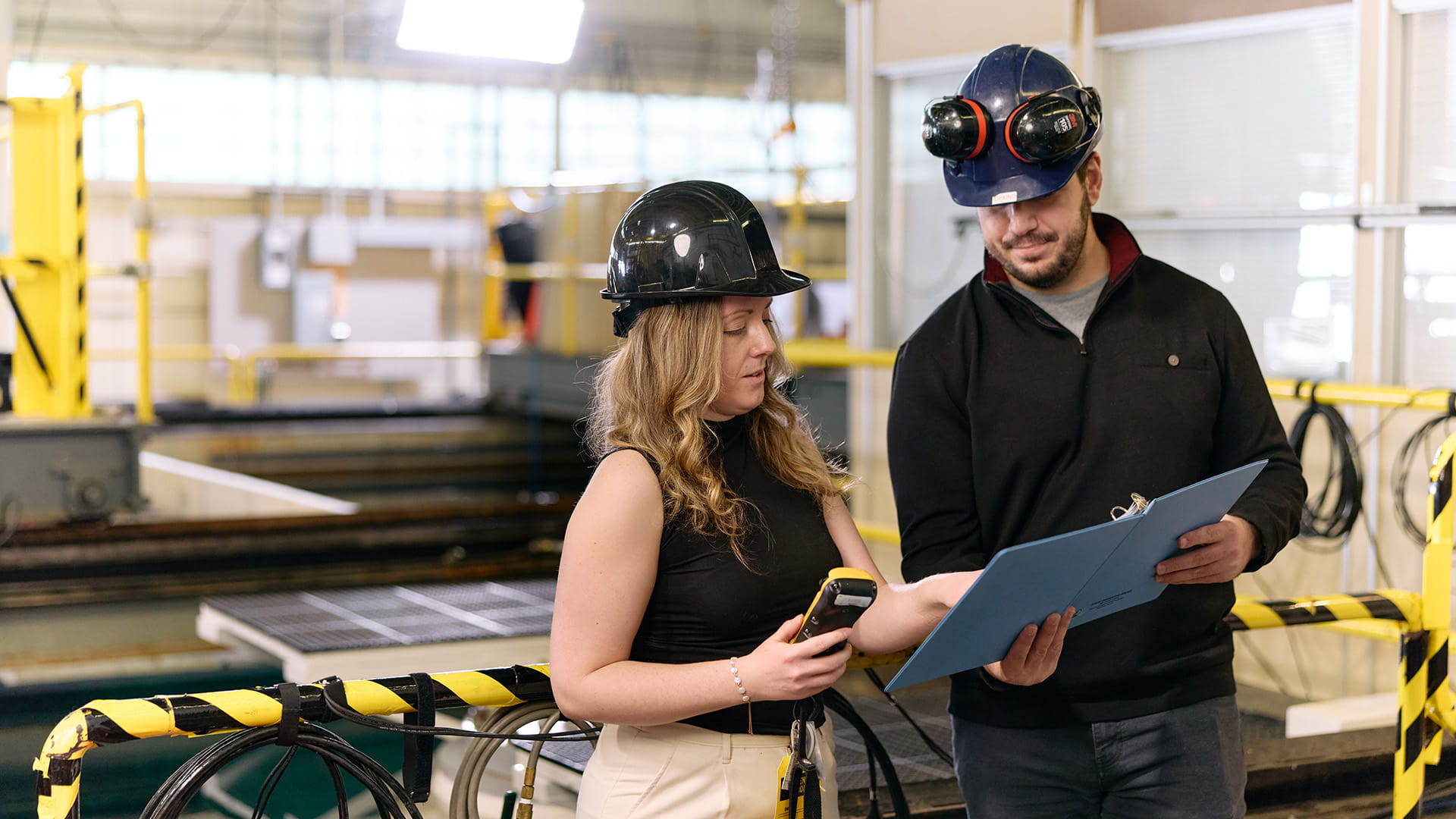
RTX is investing in facilities like the acoustic test tank in Portsmouth, Rhode Island, where upgrades will result in faster development and production of new technologies.
For Barracuda, the updated tank’s new software and hardware will allow better testing of the system’s underwater agility.
“This new fixture that we’re adding is going to have seven different axes,” Fabian said, using the plural of “axis.” “So it can flip out of the tank, it can go down, spin that way, spin this way – it’s basically like a glorified arm, which is going to allow us to be able to test devices a lot easier and quicker.”
The tank is part of a lab where Stephanie Gratiano, the hardware and production support lead for Barracuda, is focused on moving its sonar component from development to production. It’s challenging, she said, and requires collaboration with acoustic experts, manufacturing engineers and operators.
But in Portsmouth, they’re all in one place.
“It really allows for more seamless transition from an initial concept or idea and the development of that idea to working on prototypes – and then being able to pivot really quickly to perform the tests,” Gratiano said.
Gratiano has seen Barracuda evolve since she joined Raytheon in 2017. As she worked on pieces of the program, she got to see how the combination of talent and facilities in Portsmouth led to a transformative technology.
“Seeing the bigger picture really allows you to connect to the mission,” she said. “To be able to contribute to the technology that is going out into the field, hopefully saving a lot of lives and bringing those warfighters home, is very important.”