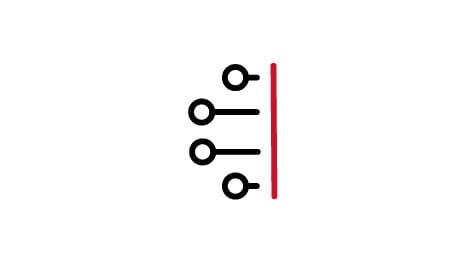
The ‘fuse box’ of electrified flight
Engineers at RTX, half a world apart, bond in building the backbone of a future plane’s power system
Inside the attached zip folder was a series of files, each holding pieces of a larger puzzle that, once manufactured and assembled, had the power to advance electric flight.
The files took only seconds to download, but for Greither, a project engineer for Collins Aerospace in Nördlingen, Germany, their contents signaled the start of a project that would consume his professional life for more than a year.
Greither and his team were tasked with building prototypes of a power distribution panel and solid-state power switch – in common terms, a circuit breaker. Together, the components would protect the megawatt electrical systems expected to fly on tomorrow’s hybrid-electric and fully electric passenger jets.
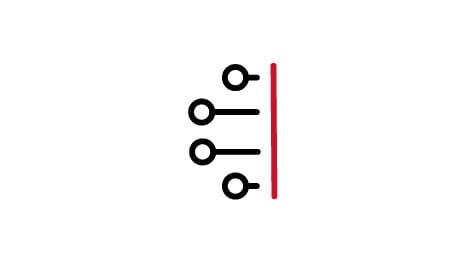
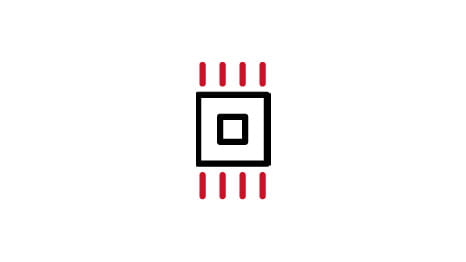
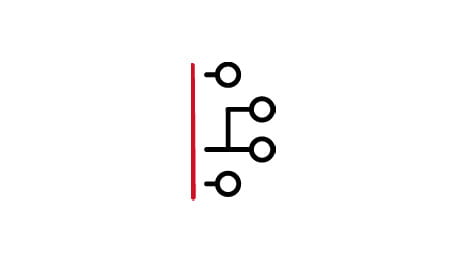
“I find it totally exciting that our company is on the forefront of this work,” said Greither, referring to the reduction in carbon emissions that electric flight promises to bring. “I’ll be very happy to send these units out and get first test results so we will see all the good things that can be done with this equipment.”
The project reflects RTX’s commitment to sustainable aviation and is one part of a broad approach to help the industry reach net-zero carbon emissions by 2050. It also reflects the worldwide engineering expertise RTX can summon when solving problems the company considers critical – in this case, how to scale up a plane’s power infrastructure to support more electric flight.
Cross-company collaboration
It all began in 2022 when Pratt & Whitney, an RTX business, was working with NASA’s Advanced Air Vehicles Program to research next-generation electrical systems on aircraft.
The Pratt team turned to colleagues at Collins in the U.K. and in Rockford, Illinois, as well as to engineers at the RTX Technology Research Center in East Hartford, Connecticut, for help. After more than a year of research, modeling and experimenting with different heat-conducting materials, the initial team had a workable solution that was ready for phase two.
Josh Swenson, senior technical fellow and principal engineer at Collins, has been part of the project since its inception. He considers the cross-company collaboration and phased approach a good example of how a research and production chain ought to work.
“We’ve moved from a hand-built proof of concept unit that shows what we can accomplish in a lab, to an early production-like version that has enough pedigree that it could potentially fly on a test aircraft,” said Swenson.
Gallery: What they built
For the team in Nördlingen, which normally makes electronics and circuit boards, the project came with invigorating challenges. Not only was the circuit breaker completely new in concept, but they also had to factor in differences between U.S. and European Union measurement standards and inspection protocols, as well as find reliable sources for the new materials and parts.
After several weeks of research, reverse engineering and consulting with other teams across RTX, Greither and the other engineers at Nördlingen created their own meticulous drawings to guide production.
Proximity is good for problem-solving
When Tino Schuldt, site lead at Nördlingen, arrived in 2023, the team was already hard at work on the “power switch” project, as it was called. Out of the 120 employees at the site, about 20 worked on the new components. Everyone else kept the day-to-day operations running smoothly.
Schuldt knew from years of leadership experience how important it was for various contributors to find common ground.
One day, right before it was time to assemble the circuit breaker, he called everyone to the shop floor.
They stood right next to the assembly line – a position that allowed them to work through any problems in real time, and also watch as their work finally took physical form.
“It’s special to be able to go down to the line, for everyone to smell the oil, see the machinery, to understand the technical aspect behind what we’re doing,” said Schuldt. “And it’s not just about the technical solution, right? We all have to understand the larger point of why we’re there.”Next stop: Further testing
Sets of the power distribution components will be delivered to a lab at a German university as part of a government-supported program to advance an aircraft powered by a hydrogen fuel cell.
Additional sets will undergo further testing at The Grid, Collins’ electric power systems lab in Rockford, Illinois.
There, experts will see how the power controller and power distribution panel handle the dramatically higher levels of electric power typical of these new aircraft architectures. Specifically, teams will pair them with two megawatt-class electric motor generators, as well as a Pratt & Whitney GTF engine.
The Grid tests are part of the SWITCH project, in support of the European Union’s Clean Aviation Joint Undertaking (Clean Aviation). In addition to Collins Aerospace and Pratt & Whitney, other SWITCH participants include MTU Aero Engines AG, GKN Aerospace and Airbus.
Change starts here
Karl-Heinz Kraut is the section lead for supply chain management at Collins Nördlingen, responsible for procurement and order handling. It was part of his job to find materials to build the electrical boards needed for the project – something that’s especially challenging when geopolitical tensions are high. Sourcing materials can’t be rushed.
“We have to be careful to use the right source from the right countries where the parts are manufactured,” he explained. “We have to look at a stable supply chain of the future.”
Finding the right suppliers in the European Union and in the U.S. challenged the team on cost and schedule. It was all part of ensuring that the components could be reproduced consistently going forward.
Kraut’s work led him to look at the smallest details of the production process, but he never lost sight of the project’s long-term goal: to advance clean aviation.
“I’m proud to be working for a company that knows the right way to make the world better,” said Kraut, an early adopter of other sustainable technologies. “I drive an electric car. I have solar panels on my house. Yes, it’s a challenge to change these things, but we must.”
“If we don’t start to change,” Kraut added, “nothing will change.”