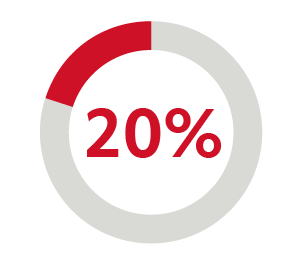
The GTF engine
Making history – now and in the future
Ben Bellows is a believer in the Geared Turbofan engine.
His Pratt & Whitney colleagues designed and built it, then watched it revolutionize commercial aviation by giving smaller planes the range to cross oceans.
“You’re lucky if you get a chance to work on something like this once in a lifetime,” he said.
And Pratt & Whitney is poised to do it again. The engine maker is working on new models of the GTF™ that will deliver better fuel efficiency and even lower CO2 emissions.
It's a story you see in every corner of Raytheon Technologies (Pratt & Whitney is a Raytheon Technologies business.) Engineers produce industry-changing technology – the Patriot air and missile defense system, the SM-3 interceptor, a galaxy of products to improve flight and secure communication across aerospace and defense – then the next generation of engineers takes what makes those products great and does it even better.
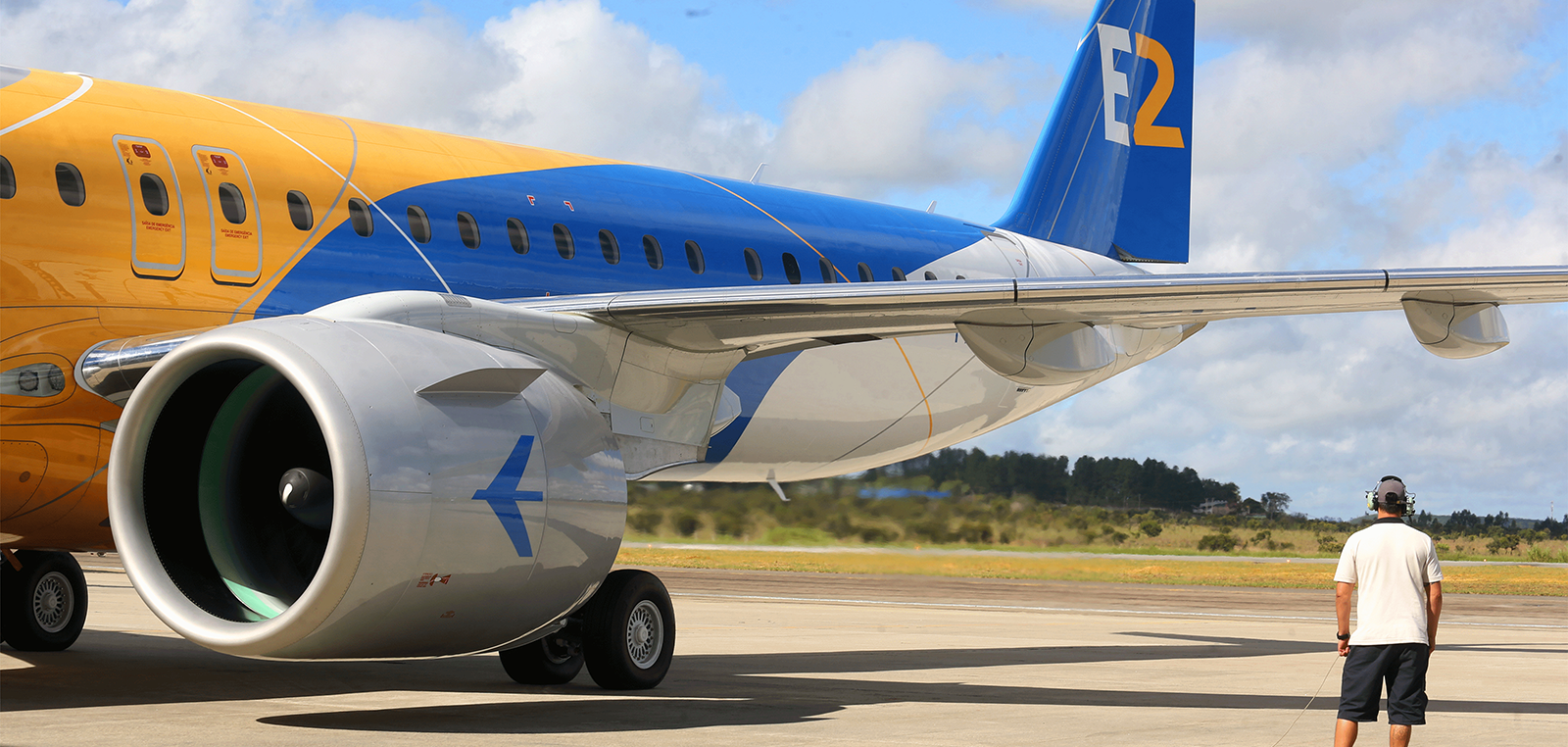
More than 750 aircraft carry the GTF engine across three families.
What makes the GTF engine great
The engine has brought greater efficiency and reduced emissions. In a conventional jet engine, there’s a fan in the front and a turbine in the back, and they move at the same speed. The trouble is that, for maximum efficiency, the fan in the front wants to turn slower than the turbine, which wants to turn quickly.
The GTF engine, by way of a gear system in between the two, makes it possible for the fan and the turbine to spin at their optimal speeds.
But that’s the technical stuff. More on that later. This is a story best told through a scene that played out on a sunny spring day in May 2016.
Teams of Pratt & Whitney employees boarded buses and headed to Bradley International Airport in Windsor Locks, Connecticut, to catch the flight of an Airbus A320neo en route to the airframer’s home base in Toulouse, France. Others watched with their teams back at Pratt & Whitney’s East Hartford site.
The GTF engine that had been at the center of their professional lives was about to make a trans-Atlantic flight – the kind of voyage once reserved for larger aircraft that burned up to 20 percent more fuel. On this day, Airbus did a flyover in Connecticut and West Palm Beach, Florida, to salute the P&W employees who helped make the feat possible.
Those engineers, manufacturing operators and support teams watching on the ground in 2016 believed in the engine, but, like Bellows, had to see it for themselves.
"So we go outside the plant that day in great anticipation. We all see it approaching, coming in lower, and it flies over our heads - and it was beautiful. But … so quiet. We weren’t used to an engine that quiet."
- Ben Bellows
His colleague, Frank Preli, said his thoughts were elsewhere – specifically, onboard the aircraft.
“If you fly on a plane with the GTF, you actually do hear noise,” said Preli, Pratt & Whitney vice president of Propulsion and Materials Technologies. “The hydraulics; not the engine. That’s not something an air traveler ordinarily hears. So passengers get the benefit of a much more comfortable ride. We can fly in to destinations otherwise not available because of reduced noise, while we are saving fuel and lowering emissions.”
Four years, 1.6 million flights and 245 million passengers later, many more destinations abound for what industry experts call a disruptive technology.
“The textbook meaning of ‘disruptive technology’ is anything that redefines the market,” said Michael Winter, Pratt & Whitney senior fellow for Advanced Technology. “And this has been completely disruptive to the marketplace as it introduced the idea of putting new engines on successful aircraft.”
Before the GTF, Pratt & Whitney was looking to build engines airlines would need for the next 30 to 50 years. Design and build took 10 years, combining the need for airlines to reduce the operating cost of each flight through better fuel efficiency, while also solving for the then-nascent awareness of climate change.
“There was an unmistakable buzz around the GTF engine program,” said Bellows, who is now senior director of Mechanical Systems, Externals, and Nacelles Engineering.
In addition to 40 industry-leading innovations, what was accomplished with the GTF’s introduction? Exactly what P&W promised.
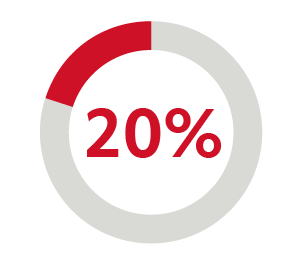
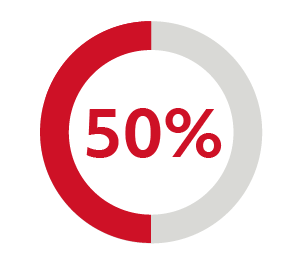
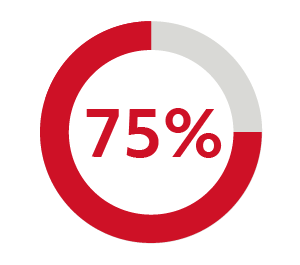
Normally it takes two generations of technology – the original and the improvement – to get these kinds of results. This time, it took only one.
Since the GTF entered into service in 2016, customers have collectively saved more than 350 million gallons of fuel. To support industry climate change targets, the GTF engine is saving more than one ton of carbon emissions every single flight hour for a total of more than three million metric tons of CO2.
More than 750 aircraft carry the GTF across three families — the Airbus A320neo, Airbus A220 and Embraer E-Jets E2 — with 48 operators enjoying more than $1 million in savings per aircraft per year. On average, a GTF engine takes flight every 50 seconds, and together they have accumulated more than 6.1 million flight hours.
How the next GTF will be better
"What is clear and proven is that the geared architecture is a game-changer for the industry, and we believe each iteration of the engine will deliver improved fuel efficiency and emissions reduction."
-Frank Preli
The early GTF designers always had future improvements on their minds.
“We built it knowing we would have a lot of runway,” said Pratt & Whitney’s Russ Grace, executive director, Engine Design and System Integration for commercial programs.
What else is possible in the future?
“Customers believe in use of the gear, and we have proven it is viable and competitive,” said Steven Johnson, senior director, Engineering- Advanced Commercial Programs. “They are asking for better performance, lower weight and lower emissions. With the GTF we have improved the fuel burn by up to 20 percent, which is 30 to 40 percent of a commercial airliner’s operating cost. The GTF took the first step towards an environmentally impactful product addressing climate change.”
Preli pointed out that GTF technology will continue to evolve over the next several years – particularly in thermal efficiency and the use of advanced materials – and that Pratt & Whitney has the next-generation single-aisle aircraft squarely in its sights.
“We’ve done this before and we’re the only ones with a geared fan today – it’s the architecture of the future,” he said.
Winter pointed out that the lessons learned on ramp-up specific to manufacturing and the supply chain will serve Pratt & Whitney well as it begins building the second-generation engine technology.
What a new GTF means for commercial aviation
“We continue to evolve the GTF architecture to allow additional speed difference between the fan and low-pressure turbine for additional efficiency improvement for both,” said Johnson. “The idea is to make a larger fan moving more air at a lower pressure rise and lower velocities out the engine exhaust. The fan is more efficient and quieter.”
A higher bypass ratio with a larger fan diameter, more advanced turbine technologies, new materials and leading-edge manufacturing techniques are in the works. And in the longer term, opportunity lies with the electrification of flight, with Pratt & Whitney and Collins Aerospace collaborating on technologies.
This collaborative effort will allow Pratt & Whitney to continue developing technologies around hybrid-electric and hydrogen-powered propulsion systems that will likely play a role in future generations of aircraft design, making a monumental impact on the industry – much like the GTF.
“Our customers are demanding even more efficient engines, not only to lower their operating costs, but also to reduce the environmental impact of flying,” Preli said. “This is a central focus for us, and we know the GTF will have a crucial role to play.”