Weaving a digital thread for the US Air Force
Digital transformation speeds development, delivery and sustainment of innovative systems
The U.S. Air Force general put it plainly: hostile nations are getting very good at fielding new technologies quickly.
“Today’s adversaries are rapidly delivering new systems and are threatening and, in some cases, surpassing our capabilities,” said Air Force Materiel Command commander Gen. Arnold W. Bunch Jr. “The increasing time it takes us to field new capabilities is our greatest hindrance to maintaining our Air Force dominance in the future.”
Bunch made those statements in support of the Air Force Research Laboratory’s “digital transformation” initiative – which includes the use of techniques such as modeling and simulation to put new capabilities in airmen’s hands at commercial-market speeds.
The digital transformation is also happening at Raytheon Missiles & Defense, a Raytheon Technologies business, where engineers are using those same techniques for the Air Force in every stage of a product’s lifecycle, from design to production to sustainment.
“We’re focused on getting superior products into warfighters’ hands quickly,” said Wes Kremer, president of Raytheon Missiles & Defense. “Digital design helps us field weapon systems faster because we can make modifications and improvements virtually and immediately test those changes. It removes a lot of the time and cost associated with traditional testing methods.”
New designs
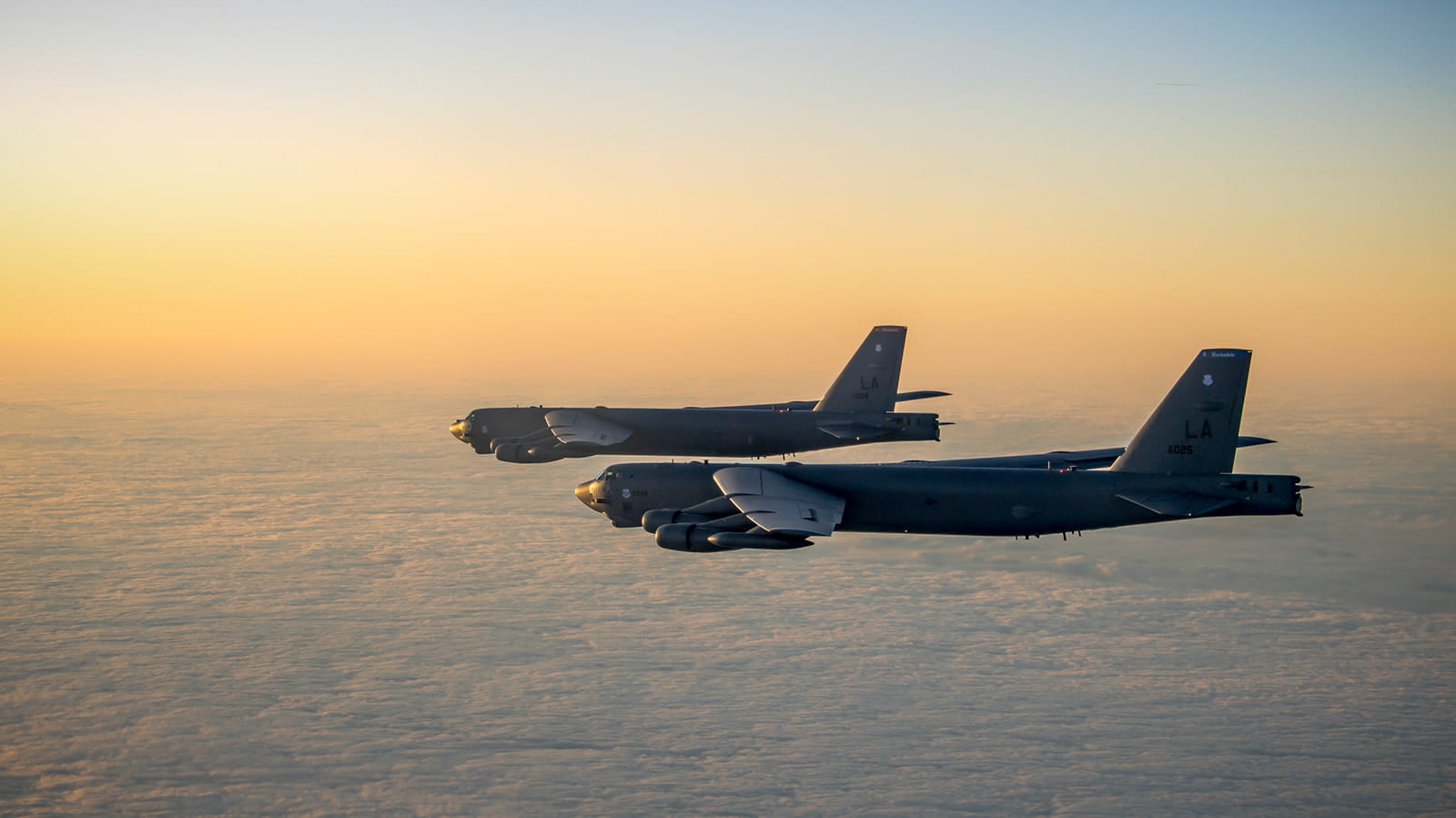
The digital transformation starts with understanding the mission and warfighter needs, which helps drive design. Raytheon Missiles & Defense is digitally engineering a new cruise missile for the Air Force that will replace the service’s legacy Air-Launched Cruise Missile. Engineers are testing components of the new weapon virtually and using feedback from simulations to inform and iterate their design.
“That approach allows us to make real-time engineering decisions that cut cost and gain schedule,” said Paul Ferraro, president of Air Power at Raytheon Missiles & Defense.
A key component of the digital thread is identifying and managing “authoritative sources of truth” for designs at any point in product development. Here’s how that looks in the design of a missile system: Every night, the digital version of the missile flies more than 6 million miles through a sampling of threat scenarios. Engineers can change modules that control the flight, including climb rate and turn speed.
They analyze results the next day, adjust accordingly and conduct further tests to see if the changes improve performance measures such as the missile’s targeting capability and survivability.
“The technologies behind virtual test environments are improving dramatically from year to year,” Kremer said. “The ultimate goal is to design and test a new capability completely in a digital environment with full confidence it will operate in the physical environment exactly as predicted.”
The data engineers obtain during testing provides a realistic and low-risk way to assess impacts on the entire system without having to build physical prototypes or install hardware.
Digital engineering and agile software development are also helping engineers create new systems such as the next-generation Global Precision Attack Weapon, or GPAW.
The small, lightweight system will specialize in defeating hard and deeply buried targets. It will fly on the F-35 Joint Strike Fighter and B-21 Raider stealth bomber, and will be compatible with fourth-generation platforms. Its open-system architecture will allow for rapid upgrades in sensing, autonomy and positioning, navigation and timing.
The GPAW system is a digital acquisition design effort, with the potential to be the first “e-Series” weapon. This means the system could be easily modified using a digital twin in a virtual environment and then physically produced.
Production
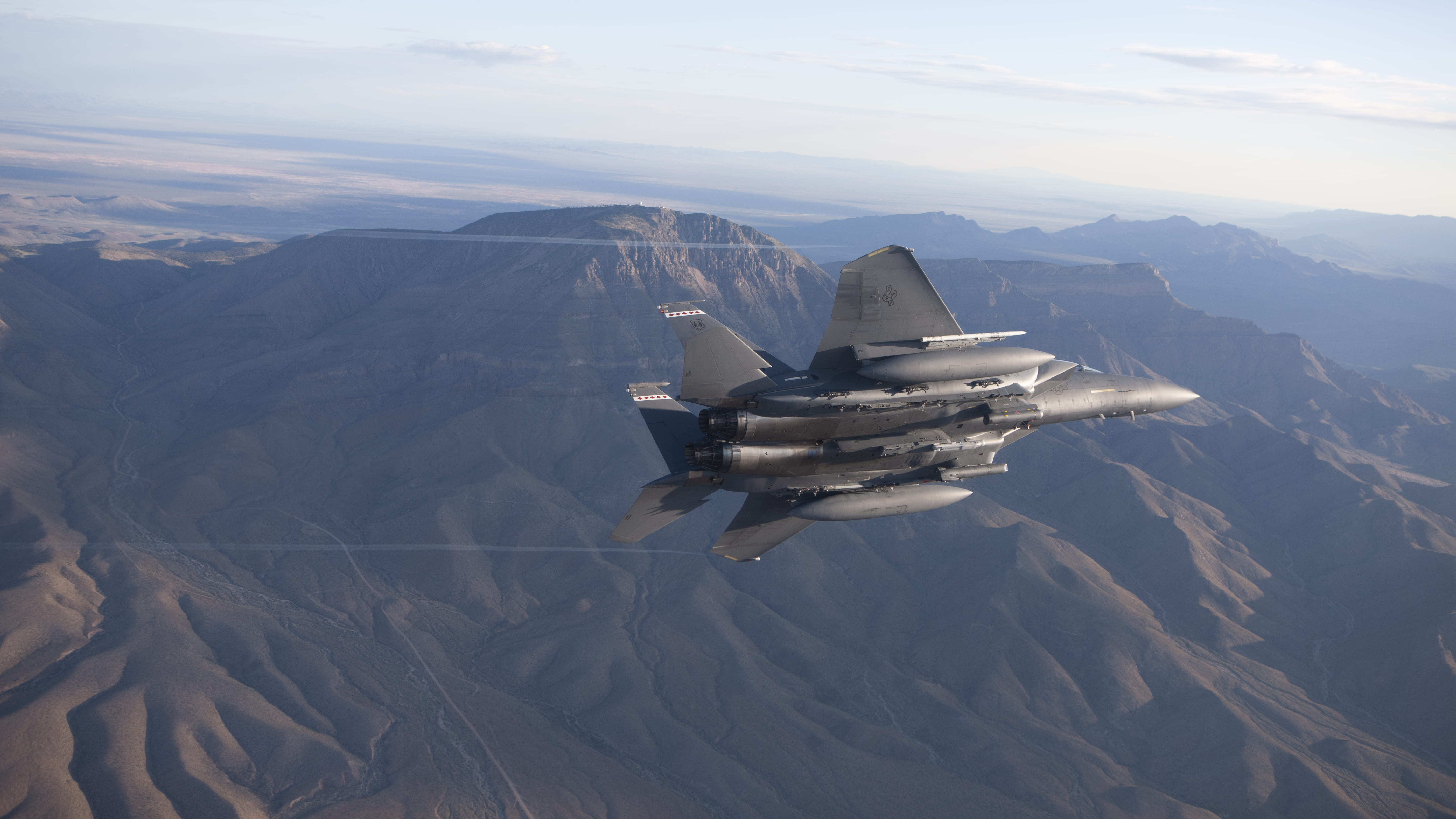
Another system benefitting from digital technologies is the StormBreaker smart weapon, which can see through fog, smoke and rain, and it can glide more than 45 miles. The Air Force cleared the StormBreaker weapon for use on the F-15E Strike Eagle aircraft in 2020.
“Emerging threats are on a shorter cycle than our design lifecycle, so digital technologies allow us to be more agile and respond to emerging threats,” said Matt Bradstreet, lead systems engineer for the StormBreaker smart weapon at Raytheon Missiles & Defense.
Digital engineering (design, production and support for sustainment) of this weapon was underway long before the Air Force transitioned to a digital acquisition structure.
“Agile software development has always been part of the core of what we do on the program. Add in modeling and simulation to prove out the capability features and you can easily see how digital transformation is a logical next step,” said Steve Milano, who leads requirements and capabilities for Tactical Strike at Raytheon Missiles & Defense.
Raytheon uses a model-based architecture for StormBreaker’s software design. The modular approach to development allows them to apply lessons learned from one product to another, offering efficiencies across the business.
To verify system performance, the team uses an integrated flight simulation, or IFS, and literally runs thousands of iterations in tandem with the Air Force.
“It [IFS] touches the core of what digital transformation tries to do – predict performance and inform the next iteration of the design,” said JD Word, technical director for Tactical Strike at Raytheon Missiles & Defense.
The benefit – time and cost savings.
“Hardware and assets are expensive. Digital clock cycles are cheap,” Bradstreet said. “We can actually reduce the number of flight tests we have to execute because our model has been validated against the flight tests we’ve already flown. That’s really a powerful tool.”
The advantages do not stop there. The business can then run scenarios in the IFS to create tactics for operational squadrons.
As the Air Force moves into the tech refresh phase for the next iteration of the system, Raytheon will look to these digital technologies to help make the StormBreaker smart weapon a true e-Series effector.
“The StormBreaker program will take advantage of the company’s more than $65 million investment in digital transformation over the next two years as we move into the next phases of the weapon’s lifecycle,” Milano said.
Sustainment
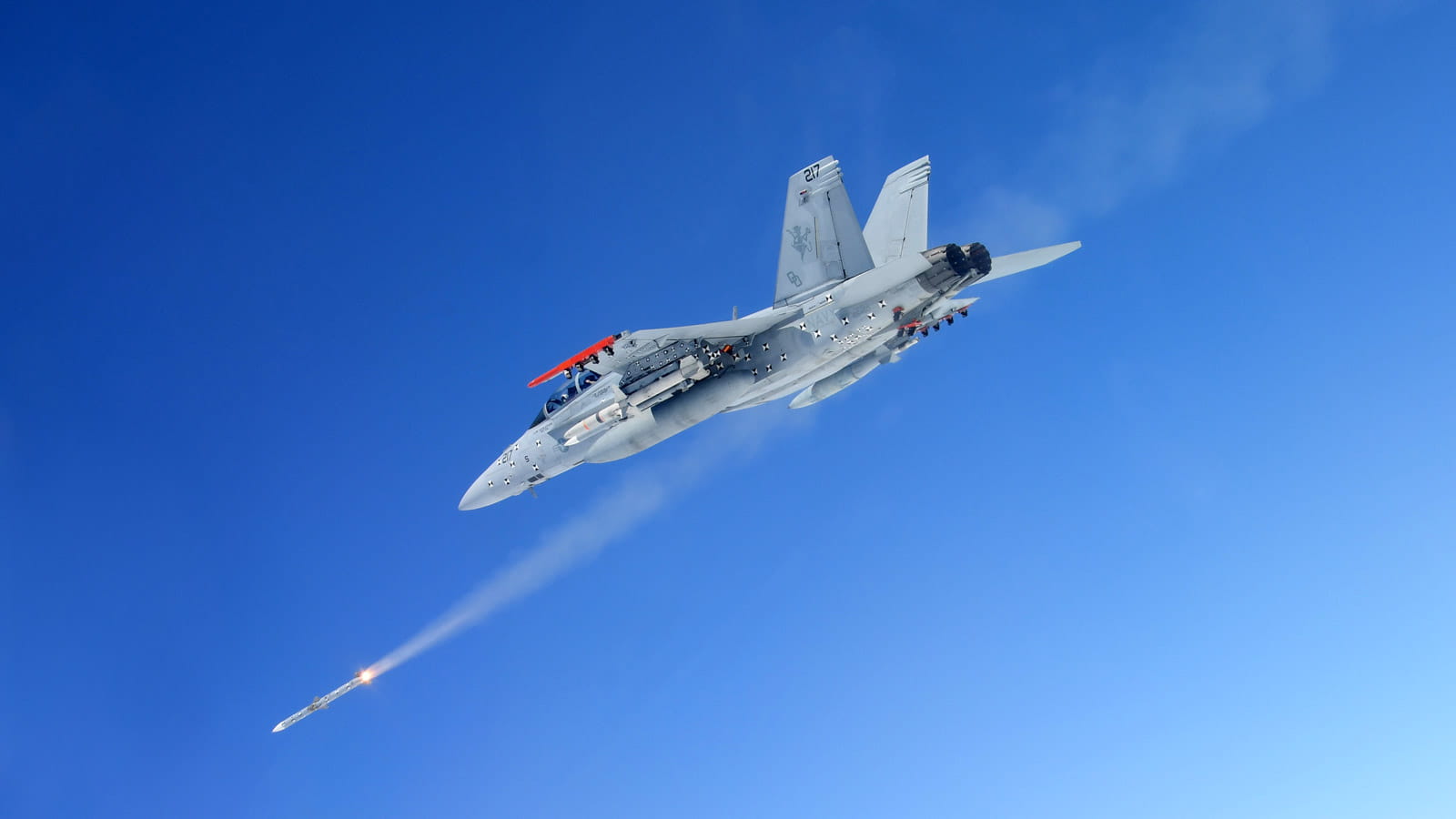
The digital thread does more than speed up design and production – it also makes maintenance and upgrades cheaper, easier and faster.
The AMRAAM missile is a radar-guided air-to-air weapon that continues to evolve with increased range, GPS-aided navigation and a two-way data link, all thanks to digital technologies.
To drive new capability into the Air Force’s primary air-to-air missile, the company created AMRAAM F3R, or form, fit and function refresh, which use model-based systems engineering initiatives.
“We were given funding to refresh the bulk of the guidance section, so we spun 15 circuit card assemblies, basically giving the missile a brain transplant,” said Jeff Zubel, air dominance lead systems engineer for Raytheon Missiles & Defense.
It allowed them to virtually try out and verify the design before procuring parts and transitioning the model into production. The company harnessed the power of knowledge sharing by using models generated by F3R to also launch a new design for its ESSM missile.
Raytheon is now working on a hardware emulation for AMRAAM’s software development to improve performance.
“We’re trying to make the conventional environment in which the warfighter operates easier to process,” said Clarence Johnson, director for air-to-air effects, requirements and capabilities at Raytheon Missiles & Defense. “It [digital simulation] leads to predictive performance for the weapon, so when an operator employs the weapon, it responds the way they expect it to – and ultimately goes out there and hits the target.”
Another way the company is using digital technologies to evolve AMRAAM is by unifying all of its requirements into a common digital database. By linking new models in development to the database, the company knows the origin of each requirement, allowing them to more rapidly troubleshoot concerns in production or adapt if requirements change.
In 2021, Raytheon received a $518 million U.S. Air Force contract to produce Lot 34 of AMRAAM missiles. The company will leverage its digital technologies to build these systems and others like its AMRAAM-Extended Range missile that provides ground-based air defense.
“Digital transformation brings us the highest tech, lowest cost and fastest product that will help us win future wars,” said John Bednarz, a senior program manager for Advanced Technologies and Air Power at Raytheon Missiles & Defense. “This is a journey we’re taking together – shoulder to shoulder with the government.”